Maßgeschneiderte tribologische Untersuchung von Hartlegierungen an Ventilen von Großgasmotoren
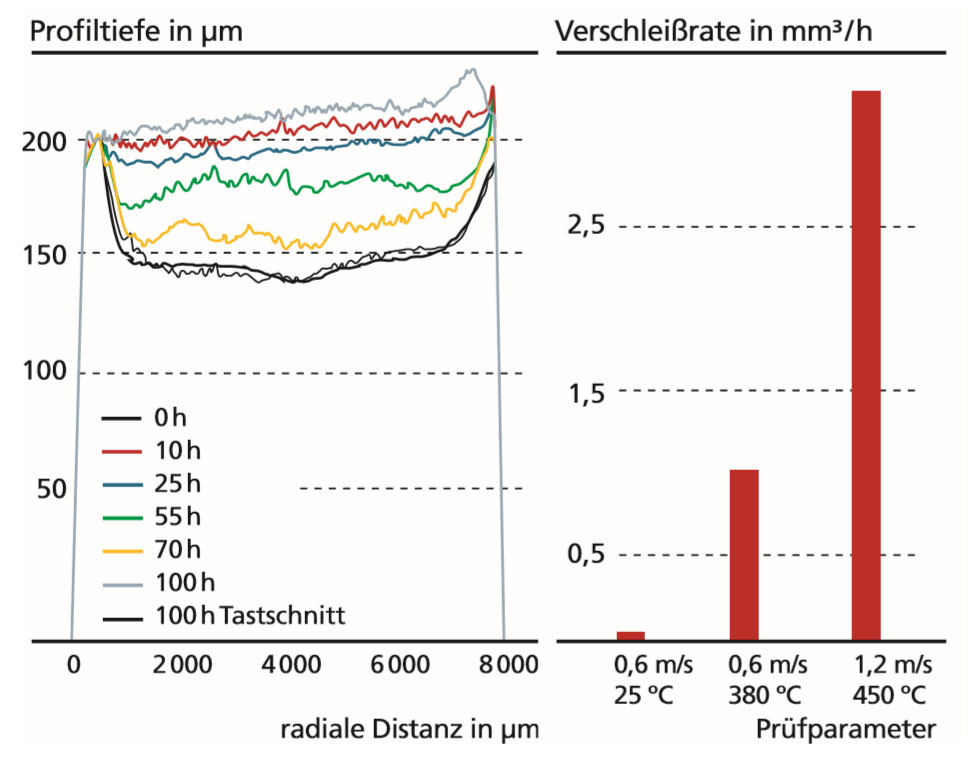
Dr. Dominik Kürten
In Deutschland unterliegt die Nutzung von Erdgas als Primärenergieträger einem stetig steigenden Trend: Aktuell steht die Energieerzeugung mit Erdgas an zweiter Stelle nach Mineralöl. Für die Stromerzeugung mit Erdgas, aber auch in der Kraft-Wärme-Kopplung (KWK), werden Großgasmotoren oftmals als stationäre Motoren eingesetzt. Um die Effizienz dieser Motoren zu steigern und gleichzeitig weniger Ressourcen zu verbrennen, werden die Betriebsbedingungen immer weiter verschärft: Höhere Temperaturen und häufigere Lastwechsel führen dabei zu steigendem Verschleiß der bewegten Komponenten im Brennraum. Aus diesem Grund hat sich der Hersteller von Komponenten und Zylinderkopfsystemen für große Verbrennungsmotoren, Märkisches Werk GmbH, zum Ziel gesetzt, seine Ventile weiterzuentwickeln und dies in Zusammenarbeit mit dem Fraunhofer IWM voranzutreiben. Die Herangehensweise an das Thema Ventilverschleiß in Großgasmotoren in dieser Art und diesem Umfang ist bisher einzigartig: In dem Projekt wurde am Fraunhofer IWM ein Prüfstand entwickelt und aufgebaut, der eine Ventilprüfung unter realen Umgebungsbedingungen ermöglicht.
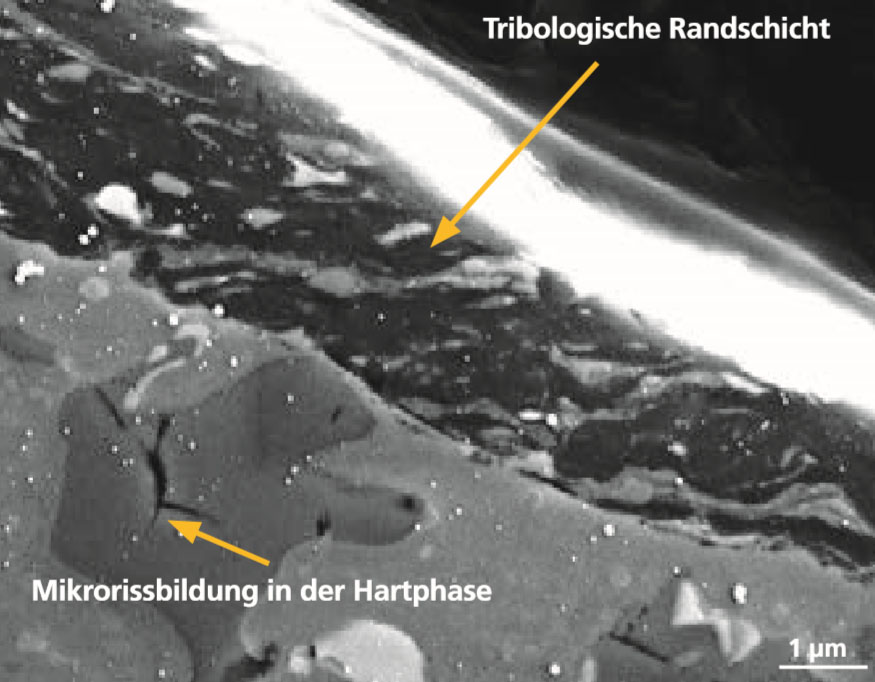
Ventilprüfung unter realen Bedingungen
Das Ziel der Untersuchungen am Fraunhofer IWM ist herauszufinden, wie sich verschiedene Werkstoffe unter den auftretenden Belastungen am Ventilsitz verhalten. Darüber hinaus sollen auch quantitative Zusammenhänge zwischen Belastungsparametern wie Temperatur, Atmosphäre, Aufschlaggeschwindigkeit sowie Verbrennungsdruck und dem Ventilverschleiß ermittelt werden. Bei Prüftemperaturen von Raumtemperatur bis zu 450 °C haben wir Untersuchungen in unterschiedlichen Umgebungsatmosphären durchgeführt. Die hydraulisch gesteuerten Schließgeschwindigkeiten können im Versuch bis zu 1,2 m/s betragen. Auf dem Bild oben rechts ist der neu entwickelte Prüfaufbau für Ventile mit einem Durchmesser von 70 bis 100 mm zu sehen. Abbildung 2 links zeigt die Ergebnisse von Profilmessungen zur Bestimmung des Verschleißfortschritts am Ventilsitz gegenüber der Belastungsdauer.
Aus diesen Messungen ergibt sich eine vergleichsweise gleichmäßig beziehungsweise lineare Zunahme des Verschleißes mit der Versuchsdauer. Somit ist es möglich, abhängig von den Belastungsparametern, Verschleißraten des Ventils zu bestimmen und diese zu vergleichen. Wir können eindeutig ermitteln, welche Belastungseinflüsse den stärksten Einfluss auf den Verschleiß haben, wo die Belastungsgrenzen der Ventile sind und welche Werkstoffe den vergleichsweise größten Verschleißwiderstand zeigen.
Stresstest zeigt die Grenzen der Belastbarkeit des Materials
Um ein Ventil extremer Belastung in einem Stresstest zu unterziehen, führten wir über einen Zeitraum von 500 Stunden einen Langzeitversuch durch: bei einer Temperatur von 450 °C und einer Schließgeschwindigkeit von 1,2 m/s. Der Stresstest zeigt die Grenzen der Belastbarkeit der Materialkombination zwischen Sitzring und Ventilstahl. Bei der Betrachtung der Verschleißraten (Abbildung 2 rechts) wird deutlich, welche Auswirkung die beiden Parameter Temperatur und Schließgeschwindigkeit auf den Ventilverschleiß haben.
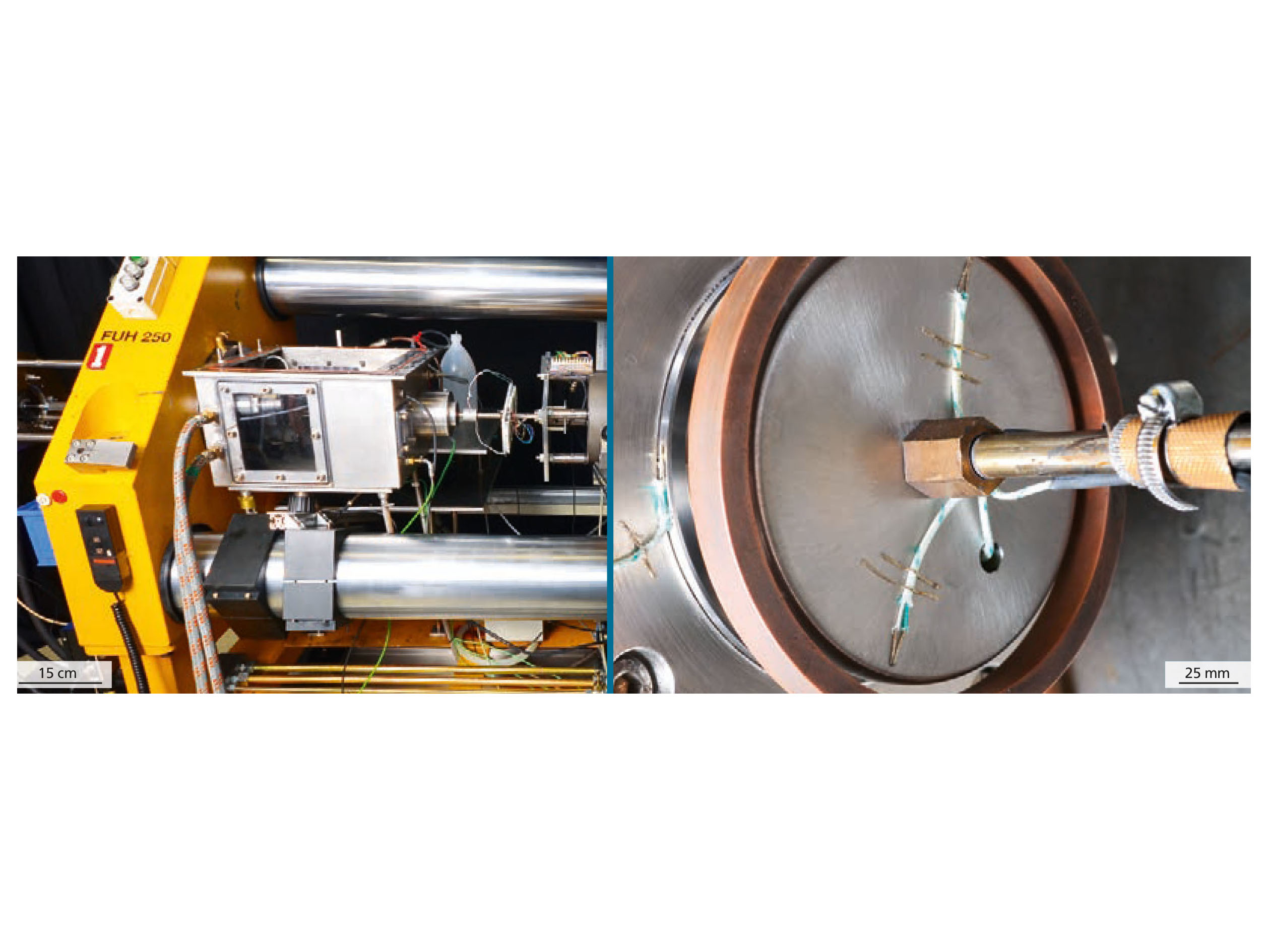
Verschleißmechanismen erkennen
Sowohl um Werkstoffe für solche Ventile gezielt zu entwickeln als auch um die Betriebsbedingungen optimal einzustellen, ist ein gutes Verständnis der Verschleißvorgänge unbedingte Voraussetzung. Verschleißanalysen, wie in Abbildung 2 beispielhaft dargestellt, ergeben hier ein klares Bild der Verschleißmechanismen: Sie zeigen, wie durch einen
Materialübertrag von dem Sitzring auf den Ventilsitz sowie die Zertrümmerung der Hartphasen im Gefüge als auch tribochemische Vorgänge tribologische Randschichten entstehen, die letztlich das Reibungs- und Verschleißverhalten und damit das Einsatzverhalten des Ventils bestimmen. Hieraus können wir wertvolle Hinweise zur gezielten Einstellung der Werkstoffe und der Betriebsbelastungen gewinnen.
Die am Fraunhofer IWM entwickelte Prüfmethode trägt mit ihren Ergebnissen dazu bei, die Belastbarkeit von Ventilen zu verbessern oder zumindest ihre Lebensdauer realistisch einzuschätzen. Diese Ergebnisse unterstützen Hersteller von Großmotor-Komponenten, Gasmotoren zu entwickeln, die durch ideal an die Werkstoffe angepasste Betriebsparameter wesentlich höhere Leistungen und Effizienzwerte bringen.