Komplett rezyklierfähiger sortenreiner Leichtbau-Verbundwerkstoff für Spritzgussbauteile entwickelt
Dr. Raimund Jaeger
Polyethylen (PE) wäre ein ideales Material für den Leichtbau: energieeffizient, auch aus nachwachsenden Rohstoffen herstellbar, nahezu rückstandslos rezyklierbar. Wirklich mechanisch belastbar sind jedoch bisher nur PE-Bauteile, die als Komposite mit integrierten Kohlenstoff- oder Glasfasern verstärkt werden. Wissenschaftlerinnen und Wissenschaftler des Fraunhofer IWM, MikroTribologie Centrum µTC, haben gemeinsam mit dem Freiburger Materialforschungszentrum und dem Polyolefinhersteller LyondellBasell nun ein tragfähiges, »sortenreines PE-Komposit« hergestellt und qualifiziert. Der Clou: Die verstärkenden Faserstrukturen bestehen ebenfalls aus PE und bilden sich sogar im Spritzguss selbst.
Die Kohlenwasserstoffe Polyethylen (PE) und Polypropylen (PP) machen gut die Hälfte aller weltweit produzierten Kunststoffe aus. PE findet sich in vielen Kunststoffprodukten des täglichen Gebrauchs. Als sortenreines Material ist es einfach und quasi unendlich häufig wiederverwendbar: gebrauchtes Produkt raspeln, aufschmelzen und zu neuen Bauteilen formen bei gleichbleibend guter Qualität. Oder PE wird erhitzt und zu Rohstoffen für die chemische Industrie oder zu Bausteinen für die Herstellung von Kohlenwasserstoffmaterialien zurückverwandelt – ganz ohne Rückstände. Darum und aufgrund ihres geringen Gewichts sind Kohlenwasserstoffmaterialien allgemein ideal für den nachhaltigen Leichtbau: beispielsweise in der Automobilindustrie, die bei ihren Produkten die Wiederverwertbarkeit zu einem gewissen Prozentsatz gesetzlich nachweisen muss.
Jedoch können aus regulärem PE bis heute keine tragfähigen Bauteile hergestellt werden, da es als Werkstoff nicht widerstandsfähig genug ist. Zur Verstärkung werden bisher Füllstoffe genutzt, besonders Kohlenstoff- oder Glasfasern. Dabei verschlechtert sich die Energie-, Rohstoff-, Umwelt- und Kostenbilanz dramatisch: Die Herstellung sowie das Recycling sind erheblich erschwert und kostspielig. Eine Alternative bietet sogenanntes ultrahochmolekulares PE (UHMWPE), das als Hochleistungswerkstoff beispielsweise in medizinischen Implantaten wie Hüftpfannen oder Kniegelenken verwendet wird. Dieser sortenreine, hochfeste und abriebbeständige Werkstoff lässt sich jedoch nicht im Spritzguss verarbeiten: Er muss aufwändig und kostenintensiv als Pulver in eine Form gepresst, gesintert und danach zum exakten Bauteil gefräst werden. Fasern aus UHMWPE können zwar die Festigkeit von Stahl erreichen, sind jedoch teuer und für ein Werkstoffrecycling ungeeignet.
Sortenreines PE-Komposit durch ein kontrolliertes katalytisches Verfahren
»Im Projekt SusCOMP forschten wir an sortenreinen Kompositen aus PE, die sich im Spritzguss verarbeiten lassen und dabei direkt selbst verstärken – besonders interessierten uns dabei natürlich, welche mechanischen Eigenschaften diese Komposite erreichen«, erklärt Raimund Jaeger, Gruppenleiter »Polymertribologie und biomedizinische Materialien« am Freiburger Fraunhofer-Institut für Werkstoffmechanik IWM. »Die Firma DSM spinnt zwar bereits Hochleistungsfasern aus langen UHMWPE-Molekülketten, die sich entlang der Faserrichtung orientieren, sogenannte Dyneemafasern.« Solche Fasern als Verstärkung in PE einzubringen wäre technisch möglich, sei aber mit einem hohen Arbeits- und Kostenaufwand verbunden und für das Werkstoffrecycling ungeeignet.
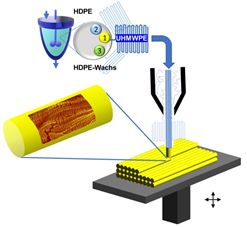
Sortenreines PE-Komposit durch ein kontrolliertes katalytisches Verfahren
»Im Projekt SusCOMP forschten wir an sortenreinen Kompositen aus PE, die sich im Spritzguss verarbeiten lassen und dabei direkt selbst verstärken – besonders interessierten uns dabei natürlich, welche mechanischen Eigenschaften diese Komposite erreichen«, erklärt Raimund Jaeger, Gruppenleiter »Polymertribologie und biomedizinische Materialien« am Freiburger Fraunhofer-Institut für Werkstoffmechanik IWM. »Die Firma DSM spinnt zwar bereits Hochleistungsfasern aus langen UHMWPE-Molekülketten, die sich entlang der Faserrichtung orientieren, sogenannte Dyneemafasern.« Solche Fasern als Verstärkung in PE einzubringen wäre technisch möglich, sei aber mit einem hohen Arbeits- und Kostenaufwand verbunden und für das Werkstoffrecycling ungeeignet.
Die Lösung für diese Herausforderung fand Prof. Dr. Rolf Mülhaupt mit seinem Team am Freiburger Materialforschungszentrum FMF der Albert-Ludwigs-Universität: Er platziert unterschiedliche Katalysatoren, mit deren Hilfe PE in verschiedenen Kettenlängen gezielt hergestellt werden kann, fein verteilt auf dem gleichen Katalysatorträger. An diesem Katalysator werden bei der folgenden Synthese des PE durch Ethylenpolymerisation gleichzeitig Mischungen aus nieder-, mittel- und ultrahochmolekularem PE hergestellt, sogenannte Reaktorblends. »Mit diesem Trick entstehen direkt bei der Polymerisation PE-Blends, die sich problemlos spritzgießen lassen«, erklärt Prof. Dr. Mülhaupt. Das Verfahren vermeidet hohe Viskositäten, die normalerweise eine Herausforderung sind, wenn ein hoher Anteil von UHMWPE-Molekülketten im Spritzguss verarbeitet werden soll. Die hohen Scherströmungen, die beim Spritzguss in schmale Spritzgussformen auftreten, sind dann dafür verantwortlich, dass sich aus den ultrahochmolekularen Bestandteilen durch Selbstorganisation des Werkstoffs faserartige UHMWPE-Strukturen ausbilden. Diese Fasern verstärken das Bauteil, orientieren sich beim Spritzguss sogar in der gewünschten Richtung und sorgen so für mechanische Stabilität. Und diese Bauteile lassen sich gut wiederverwerten: »Wir haben Proben davon insgesamt zehn Mal werkstofflich rezykliert und immer die gleich gute Qualität erhalten, da sich die gewünschten Werkstoffstrukturen durch Selbstorganisation immer erneut ausbilden«, so Prof. Dr. Mülhaupt. Proben dieses neuen Hochleistungsmaterials prüften die Wissenschaftlerinnen und Wissenschaftler am Fraunhofer IWM auf ihre Werkstoffeigenschaften hin. Die mechanischen Eigenschaften zeigen: Es sind viele Anwendungen vorstellbar, beispielsweise lange Möbelteile, Schienen- und Rolladenführungen oder Teile fürs Autointerieur. Neben dem geringen Gewicht haben die Bauteile auch den Vorteil, Schmierstoffe auf Wasserbasis sehr gut zu vertragen.
Zukünftig auch sortenreine PE-Komposite nach Bedarf
In dem Nachfolgeprojekt 3D-SusCOMP geht es nun darum, das Material per 3D-Drucker zu verarbeiten. Bisher ließen sich die guten Eigenschaften der sortenreinen Komposite nur erreichen, wenn die Polymere in einer schmalen Spritzgussform orientiert wurden. Jedoch: die Verstärkung durch Selbstorganisation erfolgt ausschließlich in der Richtung, die durch die Spritzgussform vorgegeben ist. Das ist bereits ein großer Fortschritt, allerdings sind auch andere Bauteilformen und Werkstoffe, sogenannte multidirektionale Komposite, wünschenswert. Die Wissenschaftlerinnen und Wissenschaftler fanden heraus: In der Düse eines 3D-Druckers bilden sich die Faserstrukturen ebenfalls aus. Deren Orientierung im Bauteil kann jedoch im Gegensatz zum Spritzguss über die Bewegung des Druckkopfs gesteuert werden. Hierdurch sind viele neue Anwendungen für diesen recyclinggerechten Werkstoff denkbar: neben Zahnrädern im Automobil oder für die Lebensmittelindustrie können auch sich anschmiegende Robotergreifer, medizinische Orthesen oder Steckverbinder »aus einem Guss« hergestellt werden.
Die beiden Projekte SusCOMP und 3D-SusCOMP des Freiburger Leistungszentrums Nachhaltigkeit werden vom Land Baden-Württemberg und der Fraunhofer-Gesellschaft gefördert. Grundlage bei der Katalysatorentwicklung ist eine langjährige, durch das BMBF geförderte Forschungskooperation des Freiburger Materialforschungszentrums und dem weltweit führenden Unternehmen LyondellBasell in Frankfurt.